News
2024.12.09
知財ニュース
世界初の試作成功―金属3Dプリンティングで新素材開発、自動車の車体軽量化に期待
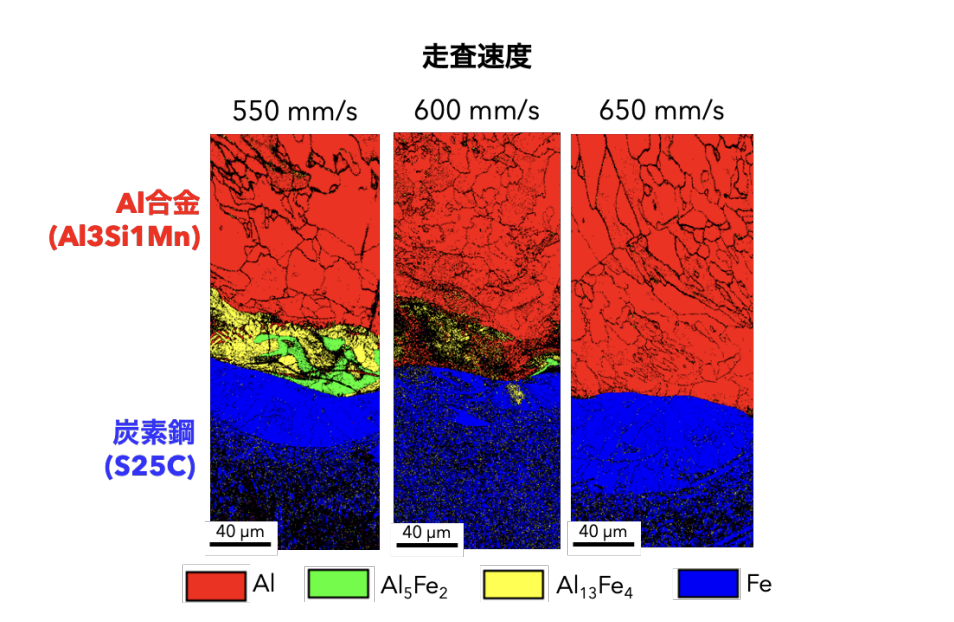
東北大学の研究グループは、2024年11月26日、金属3Dプリンターを用いて鉄鋼材料とアルミ合金を組み合わせたマルチマテリアル構造を製造するための基盤技術を確立したと発表した。
金属3Dプリンターは、金属の粉末やワイヤーを溶かしたり、高温に保持して焼結することで造形を行う。近年、金属3Dプリンターによる強度や耐食性などの材料特性を改善する組織制御を使用した高機能材料や異なる材料を適材適所で組み合わせたマルチマテリアル構造の創製に注目が集まっている。
マルチマテリアル構造は自動車や航空機を軽量化することができ、カーボンニュートラルの実現や省資源化において重要だ。しかし金属材料の組み合わせによっては異材接合界面に脆い金属間化合物が形成され、接合強度が著しく低下することが実用化の課題となっていた。
研究グループは、金属を対象とした代表的な3Dプリンティング技術の一つである「レーザー粉末床溶融結合法」を用いて、鉄鋼材料とアルミ合金の接合界面で非平衡凝固(溶融金属が熱力学的な平衡状態に到達しない状態で凝固すること)が得られることを見出した。
この研究に使用された「レーザー粉末床溶融結合法」は金属粉末に高エネルギーのレーザーを照射することで溶融・凝固し、それを繰り返すことで3次元構造体を造形する手法だ。これを用いて非平衡凝固を得られることを発見し、金属間化合物の形成が著しく抑制されることで強固な接合界面が得られることを実証した。
同研究グループは、この成果を基に、世界初となる実物大の自動車用マルチマテリアル部材(サスペンションタワー)の試作にも成功した。実用化に向け、自動車メーカー等との共同研究や実用化に発展させたいと考えているとのこと。
また、接合強度に大きな影響を及ぼす界面付近に発生する応力・ひずみの可視化・定量化が重要な技術的課題なのだという。今後は、合金種・組成や使用する粉末の形態・粒度分布、造形条件などの影響を体系的に調べ、マルチマテリアル造形技術の最適化に取り組むとのこと。さらに、本成果を同様に界面の脆化が問題となる金属材料の組み合わせに応用し、幅広い応用を目指すとしている。
Top Image : © 国立大学法人 東北大学